|
· www.tappi.org
· Subscribe
to Ahead of the Curve
· Newsletters
· Ahead
of the Curve archived issues
· Contact
the Editor
|
|
|
|
Innovation Breeds Disruption
BY GRAEME RODDEN
(The following is an excerpt of the full report, offered as an ICYMI to Ahead of the Curve readers. See links for more information at the end of the article.)
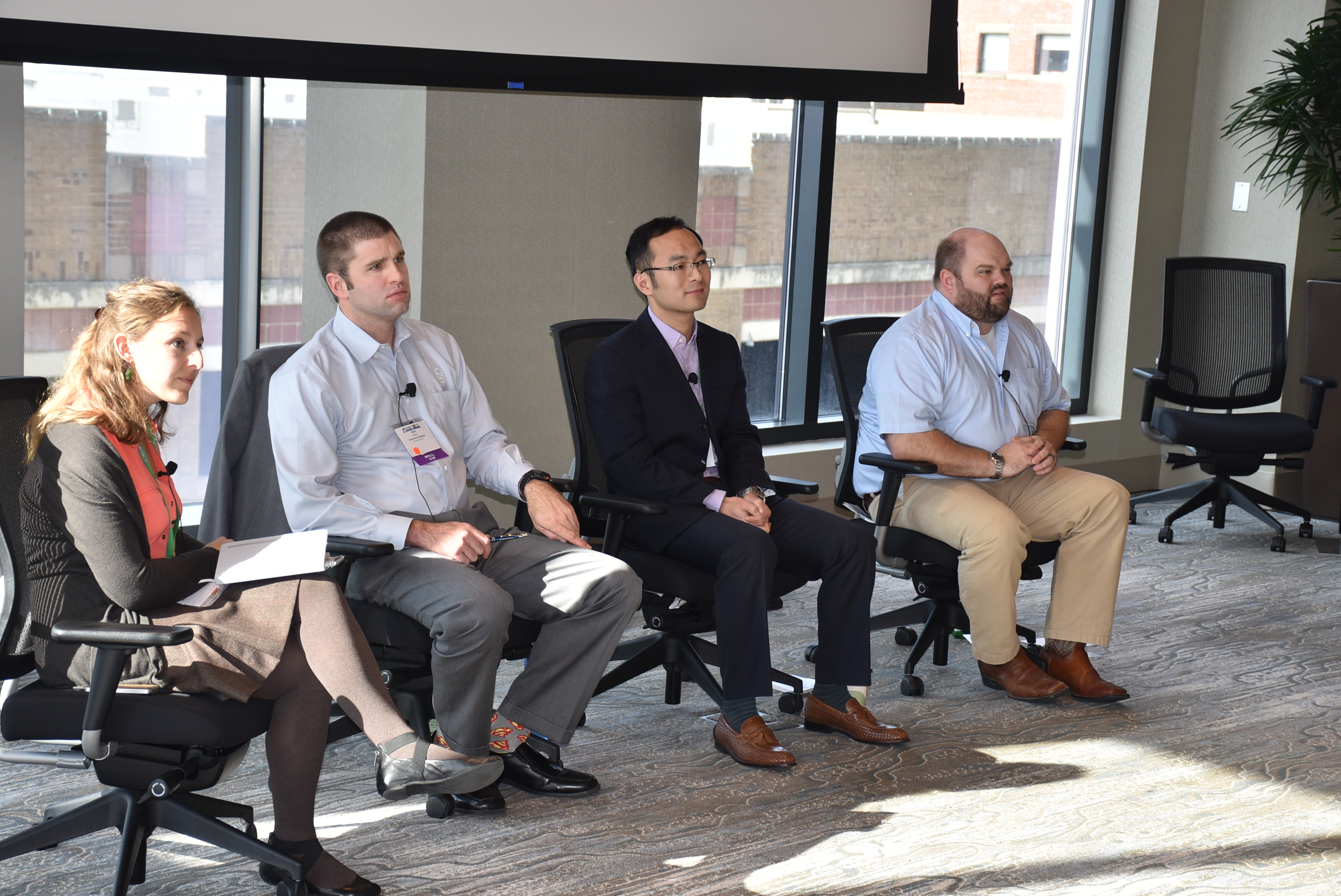
Panelists at the PEERS Conference session on Work:Life Balance.
The annual PEERS Conference was held in Norfolk, VA, in early November. Opening keynote speaker Robert Tiede, executive vice president and COO of Sonoco, set the stage early for an excellent conference with a thought-provoking talk about disruption.
He went through some of the recent changes in the US retail grocery industry: Aldi expands; Amazon buys Whole Foods; and, Lidl enters the US. “It is all disruption, but disruption is not new,” Tiede said. “It has happened throughout history, in all industries, for example the rotary phone.”
However, he added, there is no disruption without innovation. So, he then asked delegates: “What are you: disrupter or disrupted? Disrupters define who they are and what they do.How you define your business defines your chances of success.”
Tiede went on to say that stability is dangerous in a highly competitive business sector because it allows for inertia. The fundamentals of a job have not changed—but how one does it is important. “Focus on the why, not the what,” Tiede offered. “Disruption is a process that plays out over time. Disruptive companies see opportunity through a different lens.”
Accept that disruption is a given; therefore, how can one manage it. Tiede said to enhance the customer experience “in every way.” Also: “Face the right way, toward the customer.” Finally, he added, “Create an organization that can learn. Encourage curiosity, risk-taking and collaboration.”
One of the problems tends to be a bias against new ideas if there is even the slightest hint of uncertainty. (For more of Tiede’s views, see Paper360°, September/October 2017, p. 21.)
ALLIANCE FOR RESEARCH
The “State of the Industry” was given by David Turpin, Agenda 2020. However, the big news of the talk was that Agenda 2020 was changing its name to the Alliance for Pulp and Paper Technology Innovation, or appti (appti.org).
As with Agenda 2020, appti is targeting projects that would have a transformational impact on the pulp and paper industry, i.e., breakthrough technologies. Its role is to identify, inform and promote these projects. appti’s members include producers (representing 50 percent of the industry’s capacity in the US), suppliers, and associations such as TAPPI and the AF&PA.
The alliance relies on its universities partners to do the work. Thus far, the alliance has identified the following goals: reducing water and energy use by 50 percent; improving resource efficiency; and, developing new bio-based products.
To help meet these goals, appti has designed a “roadmap” and founded five teams. It built a system to create requests for proposals. It selects, funds and manages the proposals. The five teams are working on: next-generation pulping (four projects underway); black liquor concentration (four projects underway); a drier web; reuse of process effluents; cellulosic nano-materials. (For more about appti/Agenda 2020, see Paper360° September/October 2017, p. 24.)
A panel discussion followed. Attendees recognized that there is a “war” for talent. There are many opportunities for engineers in other industries, so how does pulp and paper attract and retain new talent? One challenge is that the industry is trying to get by with fewer engineers so how can it provide continual learning/development when they have such a heavy load on their plates from the get-go.
KEEPING A BALANCE
The Young Professional Division sponsored a session dealing with work:life balance. With many students in the audience, Josh Hayward, Domtar, Qiang Han, International Paper, and Ryan Henry, Green Bay Packaging, spoke of their experiences as relative newcomers to the industry. How can a “proper balance” between work and life be defined? It can be different to each individual.
A mill is a 24/7 operation. If you work (non-shift) in a mill, chances are that you can work as long as you want. No one will tell you to go home. As one panelist said, maybe someone senior should be there to advise younger workers when enough is enough. Sometimes, it takes longer than a day to complete a task. Han, who does not work in a mill setting, noted that he receives numerous requests constantly. Prioritization is critical.
It was noted that as one moves up in an organization, past “baggage” must be forgotten. One has to learn to “delegate and trust”. Newcomers soon realize that all the theories, models, etc go out the window when an emergency or urgent situation arises. As well, in shutdowns, “All else disappears.”
The panel agreed that making each shift a productive one is important. Try to learn something new every day. However, they also agreed that there is no “cookie cutter” formula for determing the right balance. The concept of loyalty to the “Company” has changed. But, “No” is still a difficult word.
A CENTURY OF CORROSION
With 10 technical tracks and 37 technical sessions, there was plenty of choice for delegates. In the equipment reliability solutions session, Max Moskal, M&M Engineering Associates, gave a fascinating look at 100 years of corrosion in the industry.
Moskal went over the changes of equipment through the years. For example, from 1940 to 1950, kraft pulping overtook sulfite and the kraft process is less corrosive. Hydrosulfite brightening was introduced, promoting thiosulfate and helping to lead to increased white water corrosivity.
Wastewater recycling began which led to a buildup of ions in the system and, therefore, more corrosion. In the 1950s, the Kamyr continuous digester was introduced and about 100 were installed between 1965 and 1970 alone.
High-pressure recovery boilers were introduced and recovery boiler explosions became an issue. Beginning in 1960, mills continued to close water systems. Recovery boiler firing was done at higher temperatures and dry solids content went from 65 percent up to 85 percent.
All of these changes led to corrosion “events” affecting batch and continuous digesters, bleach plant washers and piping, suction rolls (304 L SS) at the wet end of the paper machine, recovery boiler lower furnaces, boiler stress affected corrosion and deaerator cracking.
Unfortunately, the industry has not kept up the fight against corrosion. Moskal pointed out that there weer 47 corrosion professionals employed by the various pulp and paper research institutes between 1980 and 1990. In 2009, there were 10.The direct cost of corrosion-related issue to the industry is estimated at 2.7 to 4.7 million tons/yr, Moskal said. It is estimated that 50 percent of corrosion costs can be avoided with known technology.
In conclusion, he said that it is difficult to calculate the cost of corrosion. It is hard to justify corrosion control actions; an ROI is needed. Equipment in a mill is often replaced piecemeal. Small mills have limited resources.
For the complete version of this report, visit http://www.tappipeers.org/peers-in-review-2017/
To learn more about the 2018 PEERS Conference, which will be held October 28 – 31, 2018 in
Portland, OR, visit http://www.tappipeers.org
For a modest investment of $174, receive more than US$ 1000 in benefits in return.
Visit www.tappi.org/join for more details. |
|